- Home
- Cleaning Diagnostics
Cleaning Diagnostics
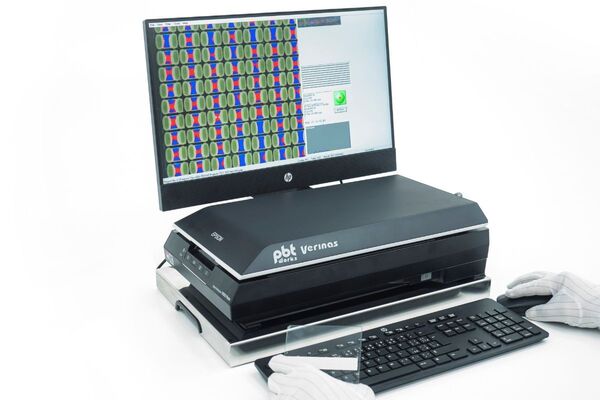
Cleaning process development
Many newcomers to cleaning technology are not familiar with important rules. The test methodology for newly established processes and product qualification is supported by standards (IPC CH56B, J- STD 001 and other). Passing following checklist (based on standards) can save a lot of time and costs.We offer tools, services and consultancy for majority of described steps.
1. Feasibility study
- Design PCBA for cleaning
- Residue characterization
- Matching cleaning agent to residue
- Material compatibility
- Cleaning machine check (machine capability)
- Rinse water quality
- Waste water disposal (limits for sewage)
2. Cleaning trials – on test boards
- Building equivalent samples (test boards)
- Optical evaluation of cleaning residues
- Surface insulation test (SIR)
- Ion chromatography
- Other test methods (surface tension)
3. Cleaning trials for product Qualification
- Optical evaluation
- Harsh environment simulation (moisture, condensation)
- Functional tests in real application
4. Qualified process stability monitoring
5. Process changes verification
- Process changes validation (see IPC J- STD 001H chapter 8)
Design PCBA for cleaning
During our nearly 30-year tradition in cleaning, we have got plenty of valuable information about challenges caused by improper component or component configuration design. We can share this information with you and help you save time, material and money to correct bad design consequences.Read more
Residue characterization
The most frequent task of PCBA cleaning is defluxing. The optimal choice of solder material (paste, liquid flux, and wire) should be made together with that testing for soldering and printing. Not every material which is optimal for soldering may also be optimal for cleaning. We can help you characterize soldering material and compare your candidates for the best suitable cleaner. We have a comprehensive library of different solder paste cleanability values, measured by unique automatic technology.
Do you need data for materials that you are using? Request more info.
Matching cleaning agent to soldering residues
Similar dissolves similar. This already medieval proverb from alchemists is still valid. Attempts to clean solder residues with other than optimal cleaner causes too long cleaning time, loss of capacity, risk of benign residues on the assembly, and damages.
Due to our unique technology, we can compare the dynamic solubility of different combination flux residues and cleaner. We can help you to clean easy and efficiently.
Material compatibility
Today, cleaning agents are sophisticated blends of many substances that are challenging to dilute a wide range of organic residues. However, cleaning chemistry can also attack materials used for component packages, insulation, or cleaning machine components. We carefully choose materials for our equipment based on compatibility testing according to rigorous internal standards. We cannot use standards for testing PCB assemblies compatibility because these are based on limited exposure by chemistry only.Cleaning machine check – machine capability
If you have an older cleaning machine, it may not have a sufficient capability to clean up-to-date electronic assemblies. We have an effective method based on Glass Test Boards and Glass Test Board Tester VERINAS to measure essential parameters: uniformity of spray nozzle impact across the entire process chamber and time-based stability of cleaning power.With the help of such measurements, we can quickly determine the cleaning machine capability Cpk.
Rinse water quality
Rinsing after the successful dissolving of flux residues is a critical operation. Enough nozzle impact or other mechanical agitation optimization must provide good penetration under components to dilute the rest of cleaner and flux residues. Rinse water quality must comply with the difficult task.Both internal water reclaim integrated on our machines or external water source must be thoroughly controlled. Besides commonly introduced conductivity measuring, we can also monitor low-ionic organic impurities with our new Organic Carbon Sensor.
Waste water disposal – limits for sewage
Every cleaning process produces waste. Before you start cleaning process it is important to know how much and what kind of waste will be generated. Also, you have to know your local limits of waste water (organic pollution – TOC and heavy metal load).Our machines can work with any waste-water conditions.
All is the question of optimization of waste processing cost. With our experiences from many processes, we can help you to find an optimal solution.
Building equivalent samples
Qualification of cleaning process requires to test surface insulation resistance (as one or more test methods for non-direct evidence of reliability – see J-STD001 H Ch.8).Different standardized PCBs are available as kits (together with components or data for manufacturing these samples).
We can supply such kits and help you with SIR tests for process characterization or qualification.
Optical evaluation of cleaning residues
Optical evaluation of residues after the cleaning is an effective method, especially for cleaning process characterization. Today, the most critical areas are under the components. Therefore it is necessary to remove components after cleaning (destructive method) for an optical check.We can perform such testing without or with only minimal damage of PCB, even for bottom terminated components.
We use preferably such method for first tests of our machines with customer´s product during cleaning trials.
Surface insulation test (SIR)
Qualification of cleaning process requires to test surface insulation resistance (as one or more test methods for non-direct evidence of reliability – see J-STD001 H Ch.8).Different standardized PCBs are available as kits (together with components or data for manufacturing these samples.)
We can supply such kits and help you with SIR tests for process characterization or qualification.
Ion chromatography
Ion chromatography is a very useful method for measuring different kinds of ionic active residues after cleaning. Even it is not a quantitative method. It offers excellent information on the possible source of residues after cleaning. In combination with SIR measurement and optical inspection, it is considered the primary test method for indirect evidence about reliability.Other test methods
A different application of electronic assembly requires applying other test methods. One very often used is surface tension measuring.For very severe conditions (like vacuum environment), also Raman spectroscopy can be applied. Another very sensitive method is gas spectroscopy of polluted inert gas flowing around the heated assembly. Such methods are sensitive to organic surface contamination, which can re-deposit in a vacuum and cause open joints.
Optical evaluation
In this phase, we check actual boards for the qualified process for cleanliness. Because the critical areas are mainly under components, our methods are targeted to check the cleanliness under components - possibly without damage to the board.Harsh environment simulation
Some assemblies must work in different harsh environments: the definition of a harsh environment is complex. It can be overexposure to any external aspect – like condensed water, salt fog, deep frost, high temperature, vacuum, sand, different toxic gases, extreme temperature cycling, radiation, and many others.The end-user must define conditions, and the manufacturer should test them.
Functional tests in real application
Such tests are necessary for assemblies, which should be qualified as highly reliable items. Typical it is in automotive electronics, but also in many other fields of transport, mining, medical electronic, avionic and other industrial application. Only tests with reap conditions and documenting all necessary parameters can give objective evidence on reliability.Process diagnostics
Once the cleaning process is qualified, we must monitor many parameters and ensure the process runs stable. The cleaning machine itself can detect not every critical parameter of cleaning. Therefore some parameters should be checked periodically in the laboratory.We can offer many of those methods to help you to keep optimal cleaning process performance.
Long term stability monitoring
The performance of your cleaning process is not a fixed value. It can change with the amount of flux residues, which you bring to cleaning. Some assemblies are less complex and have less solder. Some others are more contaminated. Sensors, even on the most advanced cleaning machines today, cannot catch these changes.We offer a simple and efficient method for monitoring the cleaning process, which can save you cost and bring evidence on the good performance at any time.
Process changes validation
According to the primary standard for assembly production J- STD-001 H, it is necessary to validate any changes in cleaning process conditions. These changes are in detail mentioned in the standard.We offer a simple method for achieving objective evidence stable performance of your cleaning process after these changes.